Janssen Takes Clinical Supplies And Patient Data From Paper To Digital

By Ed Miseta, Chief Editor, Clinical Leader
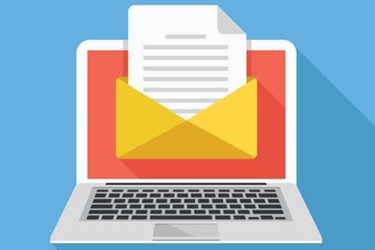
Janssen is seeking to replace paper-based, conventional processes of managing clinical supplies and tracking patient health data with a new suite of cohesive digital technologies. The new iSTEP (Integrated Smart Trial & Engagement Platform) is a technology toolset developed to automate investigative product supply and data management in clinical studies. The open approach, developed by Janssen in collaboration with technology service provider Tata Consultancy Services, is also available for use by other life sciences companies.
The pain points in clinical trials regarding medication intake and management are likely familiar to anyone involved in operations. Trials are run to determine if new medications are safe and effective. For medications to be effective, they must be taken by patients as prescribed by a physician. And yet, that intake of medicines by patients is one aspect of trials that sponsor companies seem to have the least amount of control over. It is something that is also very difficult to measure.
“Patients are generally sent home with a bottle or blister pack of medications, along with instructions on how to take the medication,” says Andreas Koester, VP of clinical innovation for Janssen R&D Operations. “Unfortunately, these instructions can be lost or simply forgotten by the patient. When a patient returns to the clinic, the only method we have of determining if they took the medication is counting the number of pills remaining in the bottle. This is an inexact and archaic process. It also forces us to include more patients in a trial than we actually need so as to compensate for patients who may opt to not take the medication as prescribed.”
Koester notes there are other pain points as well. Pharma companies are required to have accurate records that prove to regulators the final disposition of investigational medicines. This is to insure they are not used inappropriately or used outside of a clinical trial. To meet this requirement, sponsors must account for every pill that moves from the manufacturer to the investigator and, ultimately, to the patient. Unused product must also be tracked until it is destroyed.
“All of this is a very manual process,” states Koester. “Not only are we counting pills, we are manually recording the results of the count into logs, which is also a manual process. Those logs then need to be retained and eventually someone will need to sign-off when unused product is destroyed. Any process that is manual is also subject to errors. If a doctor in a busy clinic records some of that information incorrectly or hands the wrong product to a patient, the results could be deadly.”
One Comprehensive System
Researchers at Janssen felt one solution to this problem would be to have a comprehensive system or platform that addressed all of the pain points. There are solutions that have been on the market for a number of years that address some of these individual pain points. For example, there are medication scanners, smart bottles and blister packs, and even smart medications that can record when they were ingested by a patient. However, there has not been a single solution that could address all of them, and there was no way for these solutions, which were produced by different vendors, to communicate with each other. They were also not feeding data into a single database. This has limited their value to researchers and held down adoption rates.
“We were hopeful that eventually a vendor would take all of these pieces and build a comprehensive solution,” states Koester. “That did not happen, so we had to decide whether to keep waiting for one to become available or simply create it ourselves. We opted to use our engineers and our experience in this space to build the system ourselves.”
Janssen started by designing a pilot program that attempted to string several solutions together and integrate them into one platform. The first part of it involved connecting smart blister-packs to smart phones so that investigators could receive immediate feedback. Janssen then worked with patients to see if this was a technology they would feel comfortable with. The program included instructions, eLabels, and even a medicine messaging system that would remind patients to take their medications.
Finding The Right Partner
Once the pilot program proved to be successful, Janssen had to decide if it wanted to build the platform itself or if it should work with a technology partner. That decision required a good amount of reflection on what the ultimate goal of the project would be. Janssen has been active in the TransCelerate organization and other industry forums. The company believes any innovation it promotes should make trials better for all patients, as well as every pharma company conducting trials. For that reason, Janssen opted against developing an in-house solution.
“We reviewed the landscape of technology companies that we felt had the expertise and experience in clinical trials to develop this type of solution,” says Koester. “Tata Consultancy Services (TCS) is a large company with a very strong IT business. We partnered with them because they were already building solutions for clinical trials and we were confident they were interested in the solution for the same reasons we were. They saw it not as building a solution for Janssen, but a solution that would benefit all companies and all patients taking part in clinical trials.”
Feedback from patients was another big driver of this effort. The patient benefits, such as instructions, videos, eLabels, and automated reminders, were at the center of the effort. Janssen brought together a number of patients and investigators to review the prototype and get their feedback. The goal was to ensure patients and physicians actually found benefit in certain features. User feedback on language, usability, and other factors were then incorporated into the final release of iSTEP. Janssen felt there might be an issue with some older patients handling the smart phones. However, that issue did not materialize in a pilot program run by the company. A few minor tweaks, such as font size and clearer language, were necessary.
Moving forward, this is not a solution that Janssen wants to keep under wraps. In fact, it is looking to share the solution with as many companies as possible. The company proactively reached out to a number of companies last year and invited them to a workshop held in Belgium to share the specifications of the platform. Koester notes the company did this in the spirit of open innovation.
“Pharma companies know that off-the-shelf solutions can be difficult to configure to your existing processes,” adds Koester. “They can also be very time consuming. I heard that other companies have been considering similar types of integrated systems, but have not been able to bring them to fruition due to the inability to align departments internally. We received interest and feedback from a number of companies.”
Ten pharma companies also attended an open house in Belgium in June 2017 to see what progress had been made since December, and to learn how their feedback had been incorporated into the final design. Connections have already been made between TCS and other pharma companies, and according to Koester, this dialogue remains ongoing. “Making clinical trials better for patients and investigators is an effort we can all get behind,” he says.