Manufacturing Facility Will Meet Needs Of Cell & Gene Trials

By Ed Miseta, Chief Editor, Clinical Leader
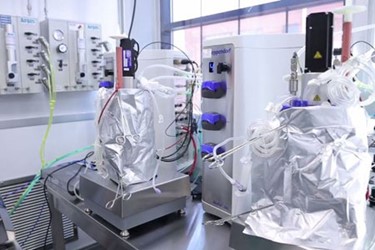
Abeona Therapeutics is developing investigational gene and cell therapies for people living with serious and rare diseases. Currently, the company is producing therapies for children afflicted with Sanfilippo Syndrome (Types A and B), two forms of Batten disease, as well as the skin condition known as Recessive Dystrophic Epidermolysis Bullosa (RDEB). Last year, Abeona held a ribbon-cutting ceremony to celebrate the groundbreaking of a manufacturing facility that is one year later producing gene therapy material for their clinical and pre-clinical programs, including lead programs EB-101 and ABO-102 for RDEB and Sanfilippo Syndrome type A, respectively. As is the norm with gene therapy, Abeona uses a virus as vehicles to deliver functional copies of defective genes.
When explaining how much virus is administered to children with Sanfilippo, company president and CSO Tim Miller likes to use the sneeze analogy. A sneeze from a person with the common cold releases about 100,000 viral particles into the air. Abeona’s treatments for Sanfilippo Types A and B, which are designed to be administered to patients in a one-time 15 to 45-minute infusion containing a quantity of viral particles that is equal to a person sneezing 10 million times per day for an entire year.
“That is an incredible amount of virus that has to be created to treat just one child,” says Miller. The amount of virus that has to be created, concentrated, and bottled takes time, is expensive, and requires expertise. Unfortunately, there are not many places in the world that can produce the product successfully. For that reason, and because of the success we are seeing in our trials, we felt it was the right time to bring the manufacturing of our adeno-associated viral (AAV)-based gene therapies in-house.”
Video Copyright and property of Abeona Therapeutics.
Historically, gene therapy manufacturers have produced various types of viruses. But Miller notes AAV is like the new kid on the block. As the use of AAV has increased, the virus has become a valuable commodity. Miller says the high demand, coupled with the low supply, has resulted in bottlenecking at contract manufacturing organizations.
“Bringing the manufacturing in-house is simply a way for us to control our own destiny and manufacture multiple products from concept to commercial,” says Miller. “If you are going to take a product like this from dishes in the lab to small and large animal models, to human clinical studies, and finally the commercial space, I personally believe you need to have your own facility.”
A Difficult Transformation
Other pharma companies (Bluebird, Novartis and Pfizer, for example) have also invested in their own manufacturing facilities. Several small cell and gene therapy companies are also pursuing the same route. In the past, Abeona used a mixed model that involved outsourcing to manufacturing vendors and academic institutions. Miller viewed bringing manufacturing in-house as the next logical step.
“As we continue to expand our vector platform to incorporate new programs, the need to go from preclinical to commercial has to be within our control,” states Miller.
Tim Miller, Abeona |
Creating the facility was not an easy endeavor. The virus production facility was built in an older manufacturing building with cement floors and brick walls. When I toured the space, it reminded me of the abandoned manufacturing facilities that you see in many large U.S. cities. That space is now a state-of-the-art gene and cell therapy manufacturing facility with new floors, white walls, glass partitions, clean rooms, and cGMP capabilities incorporated throughout. The completed initial stage of the facility, which can produce both cell and gene therapies, is 6,000 square feet. Abeona has started the buildout of an additional 20,000 square feet of laboratory space for quality control, process and assay development needs.
“When creating a new facility, you can build it from scratch or convert old space,” notes Miller. “We already had manufacturing experience in-house, and with that experience and the facilities we retained, it seemed the best option was to retrofit the available space, with a focus on capacity. We continue to advance our manufacturing capabilities for our AAV-based gene therapies and expect to be at scale for GMP production this year.”
Gene-Corrected Skin Sheets Help Children With RDEB
In addition to the AAV-based gene therapies being created for Sanfilippo and Batten patients, the new manufacturing facility is currently producing a gene-corrected cell therapy for children and adults suffering from RDEB, a rare connective tissue disorder present at birth. Patients with RDEB have a defect in the COL7A1 gene, leaving them unable to produce Type VII collagen that helps anchor the dermal and epidermal layers of the skin. RDEB manifests itself as blisters and wounds that appear on a child’s skin and generally do not heal. The blisters can turn into chronic, open wounds that can persist for weeks, months, or even years, into adulthood. That, in and of itself, can be lethal. But because of the disease, children afflicted with RDEB are also prone to getting aggressive squamous cell carcinoma, a form of skin cancer.
Abeona Therapeutics expects to initiate a pivotal Phase 3 clinical trial evaluating the potential of EB-101 for the treatment of RDEB in mid-2019 that involves the use of autologous keratinocyte sheets harvested from a biopsy of healthy tissue. The company will produce EB-101 for the trial in its manufacturing facility, which it counts as a major step forward for this clinical program and in strengthening control of supply, timelines and costs.
It is also working toward securing FDA GMP validation to produce commercial supply of EB-101 and believes that investing in CMC preparations could facilitate a smoother, more expeditious transition towards BLA filing and commercialization.
The EB-101 treatment uses a patient's own skin cells, which have been genetically engineered in a lab to express Type VII collagen. After being expanded into sheets, the corrected cells are then transplanted back to the patient.
The skin grafts are an autologous tissue that has been genetically modified. First, a skin biopsy is taken from a patient. Abeona will grow keratinocytes (an epidermal cell that produces keratin) from those biopsies. The keratinocytes are then modified with a retrovirus. Finally, scientists confirm the gene of interest (Type VII collagen) is now being expressed.
The skin patches are approximately five centimeters by seven centimeters and are living skin patches. Eight patches are produced at a time. Two of the patches are used for quality control and the remaining six are applied to wounds on the patient. The complete production process takes up to 26 days. In a Phase 1/2 clinical trial the treatment has been well-tolerated, and patients have experienced significant and durable wound healing.
Get It Right The First Time
While the patches do not cure patients of RDEB, they do repair areas where a patient may have severe wounds or blistering. As new blisters and wounds develop on a patient, additional patches can be transplanted. When the procedure is first performed, some of the cells from the patient can be placed in storage. Looking into the future, in a commercial setting, when additional patches are required, the process has the potential to be performed more rapidly and efficiently by using the patient’s stored cells.
RDEB is considered a rare disease, and there are hundreds of children alone dealing with the condition. The company is currently working on a packaging process that will allow it to be shipped across the country to be transplanted onto patients at academic centers.
“We are discovering new ways to treat these children and make a difference in their lives,” adds Miller. “Our science is what makes this possible, and we are in uncharted territory. The last thing you ever want is a doctor calling to say a patient is ready to be treated, but they can’t use your product. Your product is made for that specific patient on that specific day and we are committed to ensuring that patient benefits from a treatment like EB-101.”