Use eTMF To Navigate FDA Inspections

By Ed Miseta, Chief Editor, Clinical Leader
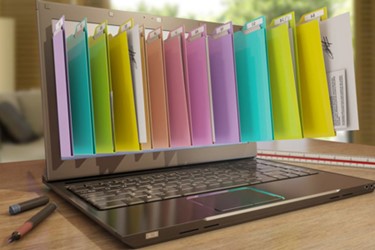
As the director of clinical operations for Allakos, Brent Sorrells spends most of his time overseeing trial master files (TMFs). He also provides logistical support for the company’s clinical trials, supports the supply chain, manages the IRT systems, and is the point of contact for the quality group. But he will tell you his primary objective is really making sure the company is prepared for its next FDA preapproval inspection.
“Being inspection-ready means making sure the TMF is up to speed,” says Sorrells. “During a preapproval inspection in 2015, we learned quite a few things. The FDA inspector followed the BIMO (Bioresearch Monitoring Program) guidance to a T, going down the list in order and making various requests. One of the primary things I learned is that we were not as organized as we had thought, even though we had done a dry run of an inspection after our NDA filing.”
Allakos had completed one clinical trial using a paper TMF. Subsequent to that, it installed Veeva Vault, an electronic TMF (eTMF) to hold its trial documents. Although the main scope of the inspection was the earlier study, Sorrells soon found himself wishing that all the company’s documents were in Vault eTMF.
Reports Help Track Documents
The BIMO guidance are the FDA's instructions to an inspector when visiting a site or sponsor. BIMO Guidance 7348.810 governs inspections of sponsor companies. Part III of this section is around 24 pages and describes what inspectors require.
One of the tools Sorrells uses for inspection readiness is the Expected Document List (EDL). The EDL lists items that are not properly matching in Vault eTMF when the Match Now operation is run. In other words, it notes what documents are needed but not yet present at different stages or milestones of the study. From the EDL, Allakos creates a list of planned documents which will pre-populate the metadata.
“The EDL will tell us we need a medical license,” says Sorrells. “The metadata in the planned document will tell us we need a medical license for Dr. Smith. From the planned documents, we can also create upload requests. We will assign either the project manager or the CRA the task of getting us the document from that site. The task is assigned to the CRA or project manager who was responsible for that document.”
Sorrells also likes to create reports using Vault eTMF. He has created a report that's customized for each CRA. CRAs receive the report about every two weeks. The report lets CRAs know exactly what is outstanding based on their site assignment. The project manager on each study is cc'd so they can monitor the progress of documents coming in. Once CRAs know what documents are needed, follow up letters are sent to the site so it is aware of what the CRA will be asking for on their next visit.
In addition to reports, Allakos also uses dashboards to track documents. Those dashboards provide executives with the status of ongoing trials, note progress made in collecting documents, and indicate where there may be quality issues.
“The dashboards will show the requests outstanding for each CRA,” notes Sorrells. “Therefore, if a certain CRA has numerous documents outstanding, I will know they are very bad at getting documents or they have a heavy workload and perhaps need some help.”
Getting Inspection Ready
Sorrells likes to differentiate between inspection preparedness and inspection readiness. He defines inspection readiness as the day-to-day activities required to ensure a complete TMF. It involves actively identifying the documents needed for the TMF. It also involves requesting those documents, collecting them, and ensuring their quality.
Inspection preparedness is broader. It encompasses not only the content that will be needed for an inspection, but also the processes around the collection of those documents. This not only includes what's within the TMF, but also the requests that are going to come from an inspector.
“In preparation for an inspection, we created a BIMO reference guide,” states Sorrells. “We went through the BIMO guidance and looked at all the requests. We figured out what was going to be applicable to us and identified 98 potential inspector requests. In those 98 requests we identified over 125 different document types we would need to generate in order to satisfy the requests.”
Once Sorrells identified what content would be required by an investigator, he had to figure out where those documents resided. He learned approximately 80 percent of the required documents resided in the TMF. A total of 43 reports were created that would enable employees to quickly extract those documents when needed.
“This is not as much work as you might think,” notes Sorrells. “If you will be going into an inspection anytime soon, going through the BIMO guidance is a good best practice. It will help you understand what the inspector will want to look at. Knowing ahead of time where that content is located will also save you a lot of time during the inspection and alleviate headaches. It took our team about a week to go through the guidance. It took a couple more weeks to determine what content we would need to generate.”
Although this process is helpful for inspection preparedness, going through 43 reports to check on the status of content is not an ideal solution. Therefore, Allakos created a dashboard for each section of the BIMO guidance. For example, Section E of the BIMO guidance relates to selection and monitoring of clinical investigators. With the dashboard, Sorrells can quickly determine the status of an entire BIMO section.
The reports will help Allakos track the status of the 80 percent of required content that resides in the TMF. For the other 20 percent that is not in the TMF, Sorrells had to identify who in the organization controlled that content. Once those individuals were located, they were informed of the inspection content that might be required of them. Sorrells worked with them to ensure they could quickly provide that content on demand. “We are not just preparing our clinical team for inspection,” states Sorrells. “We are preparing the rest of the organization for inspection as well.”
It’s Inspection Day!
Once you are properly prepared for an inspection, the final step is surviving it. When you receive notification that an inspector will be arriving in the next 10 days, it is time to put your plan into action. Your legal and quality assurance teams will play a role, so they should be notified. If you have the time, Sorrells recommends performing a full mock inspection. If you don't have the time, at a minimum, you should perform a walkthrough. This is especially important if some team members have not previously been through an inspection. Also notify other departments that may be called upon to submit content.
“This is go-time,” says Sorrells. “Decide what room is going to host your inspector. Ideally, you don’t want them to have to navigate a maze of cubicles. Seeing one employee’s messy desk could easily cause an inspector to form an opinion of how well organized your company is before the inspection even begins. You should also prepare a ‘war room.’ This will be the room where people supporting the inspection will be housed. It’s an area where participants can have open conversations about the inspection and get organized. This is where all the chaos will happen. Keep it separate from the inspection room but have a plan for how the two rooms can best communicate.”
There are many tools available to facilitate communication. For smaller companies that are not tech savvy, Sorrells recommends WebEx. A scribe can be used to take minutes during WebEx meetings, so individuals in the war room can see the document populating in real time. The messaging function can be used to seek clarity on a request or to summon employees from the war room to the inspection room. “I'm sure there are more sophisticated options, but if you're a small company without a lot of resources, you have to use what you can afford.”
When the time comes to select your scribe, Sorrells recommends you choose that person carefully. They should be able to type fast and clearly. They should also be aware of clinical terminology. If not, they will be asking a lot of questions about acronyms they don’t understand. In the inspection room you should also have a representative from regulatory and quality assurance. Someone from the clinical team should be leading the conversation and responding first to questions from the inspector. There should also be a lead person running the war room, ensuring all documents are reviewed before being handed over to the inspector. That individual will verify the documents being handed over are pertinent to the request being made.
Inform Your Partners
Sorrells has a few additional bits of advice. When you know the dates of the inspection, make sure you inform the entire office. At a previous company, Sorrells states employees became aware they had been acquired by another company and were celebrating in the hall while the inspection was taking place. “Everyone needs to be reminded to conduct themselves professionally while the inspector is on the premises,” he says.
Sorrells also suggests informing your key sites about the timing of inspections. While it is not necessary to inform every site, key sites and key vendors should be notified. “There is a pretty good chance that you will have to request additional documentation from them during the course of the inspection,” he says.
Finally, Sorrells recommends having one person manage the documents. That individual will maintain a copy of every document that goes into the inspection room. “It does not have to be anything incredibly formal,” he adds. “The method that works best for us is to take a copy of every document and place it face down in a storage box. Keep doing that throughout the day and at the end of the day take the stack, flip it over, you will have everything in the order that it was sent into the inspection room. If you get questions about a document at a later date, you can go back and see exactly what was handed to the inspector. If there is an issue with a document, you might even be able to identify it before they do. At the end of the inspection the copies can be archived.”